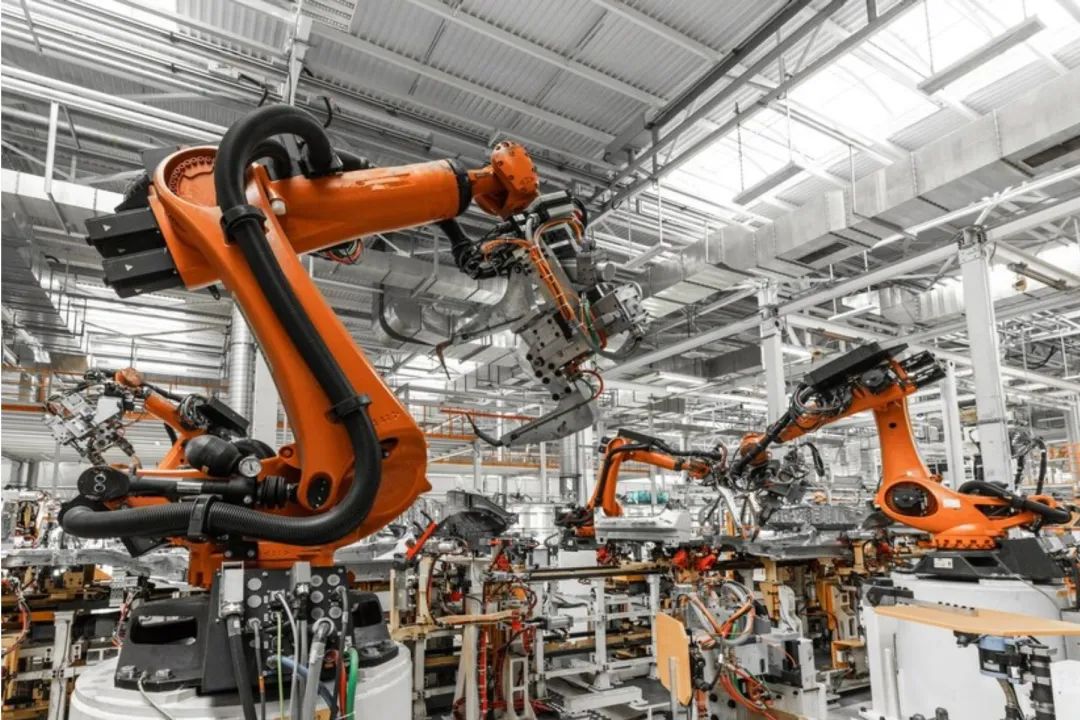
In modern manufacturing, the assembly system is a key link, which directly affects production efficiency, product quality, and flexibility. With the diversification and personalization of market demand, traditional assembly lines can no longer meet the needs of production flexibility and efficiency. Flexible assembly systems have emerged and become an indispensable part of the manufacturing industry. This article will discuss in detail the difference between flexible assembly systems and traditional assembly lines, and deeply analyze the advantages of intelligent flexible assembly systems.
1. The basic concept of traditional assembly lines
Traditional assembly lines usually refer to assembly methods based on fixed production processes. Traditional assembly lines mainly complete the assembly of products through a series of standardized production steps. Each link of each production line is usually fixed and designed for specific products. Therefore, the production process of traditional assembly lines is relatively stable and orderly, which is suitable for large-scale, single-product production.
The characteristics of traditional assembly lines include:
High efficiency: Due to standardized processes and high automation, traditional assembly lines can complete the production of a large number of identical products in a short time.
Low flexibility: Each link of the assembly line is highly dependent on fixed processes and equipment, and it is difficult to adapt to frequent product changes or diversified production.
Large equipment investment: In order to achieve large-scale production, traditional assembly lines require a large investment in fixed equipment and tools, which makes the initial investment cost high.
2. Basic Concepts of Flexible Assembly System
Flexible Assembly System (FAS) is an assembly method designed to meet personalized and diversified production needs. Unlike traditional assembly lines, flexible assembly systems achieve high flexibility and scalability in the production process through flexible and adjustable equipment, modular work units, and intelligent control systems. It can be quickly adjusted according to different product requirements and is suitable for small-batch and multi-variety production environments.
The characteristics of flexible assembly systems include:
High flexibility: Flexible assembly systems can quickly adapt to the production needs of different products, even small-batch customized production, by adjusting work units and production equipment.
Modular design: Equipment and production units can be modularly configured and rearranged as needed, greatly improving the adaptability of the production line.
Intelligent control: Modern flexible assembly systems usually combine robotics, artificial intelligence, and big data analysis to achieve automation and intelligent control of production processes.
3. The main differences between flexible assembly systems and traditional assembly lines
Production flexibility: The biggest feature of traditional assembly lines is efficient and large-scale production, which is suitable for mass production of the same products. Flexible assembly systems emphasize flexibility and can adjust production configurations according to demand during the production process to meet the needs of different products and small-batch production. For example, when market demand changes, the flexible assembly system can quickly switch to the production line of new products by reprogramming and adjusting the production unit. In contrast, once the traditional assembly line is built, it is difficult to adjust and the production line needs to be redesigned and remodeled.
Equipment investment and maintenance costs: In traditional assembly lines, due to the fixed nature of equipment and process flow, the equipment investment is high, and in order to maintain the efficiency of production, the equipment needs to be maintained regularly. The maintenance and equipment replacement of traditional assembly lines usually take a long time and cost a lot. In contrast, the flexible assembly system uses modular equipment and intelligent control systems, which can be flexibly adjusted and combined according to production needs. The equipment investment cost is relatively low, and maintenance and updating are relatively convenient, which reduces the long-term operating costs of enterprises.
Production cycle and efficiency: Traditional assembly lines usually complete production tasks through automated equipment and assembly lines, with short production cycles and high production efficiency. However, this high efficiency is usually based on the large-scale production of single, standardized products. The flexible assembly system can cope with small batch and multi-variety production while ensuring production efficiency through intelligent and automated collaborative modes, greatly shortening the production cycle and reducing waste in production.
Manual intervention and intelligence: On traditional assembly lines, although some links use automated equipment, most production processes still rely on manual intervention, especially when products are changed and adjusted. Flexible assembly systems greatly reduce manual intervention through highly intelligent control. Using robots, artificial intelligence, and big data analysis, flexible assembly systems can monitor and adjust production status in real-time during the production process, automatically complete quality inspections and problem diagnosis, and improve production accuracy and reliability.
Ability to adapt to market changes: With the continuous changes in market demand, traditional assembly lines have weak adaptability. Once the production process and equipment are fixed, it is very difficult to adjust, especially when facing small batches and multiple varieties of production needs, the disadvantages of traditional assembly lines become apparent. Flexible assembly systems can quickly respond to market changes through flexible configuration and intelligent scheduling, and realize product diversification and personalized production. This adaptability enables companies to better cope with market fluctuations and enhance their competitiveness.
Demand for production personnel: Traditional assembly lines usually require a large number of operators to perform manual operations and adjustments, especially when problems arise, and manual intervention is required. Although automated equipment can reduce some of the labor demand, it still relies on manual operation overall. In the flexible assembly system, the demand for labor is greatly reduced, the system has a high degree of intelligence and automation, and most operations can be completed by robots and intelligent systems. This not only reduces labor costs but also improves the stability and reliability of production.
4. Advantages of flexible assembly system
Improve production efficiency: By flexibly adjusting the production line and intelligent control, the flexible assembly system can improve production efficiency and shorten the production cycle.
Reducing production costs: The modular design of the flexible assembly system reduces the cost of equipment investment and can be flexibly adjusted according to production needs, reducing unnecessary waste of resources.
Support customized production: Adapting to the production needs of multiple varieties and small batches, enterprises can flexibly respond to personalized orders and enhance market competitiveness.
Intelligent operation: Using robots, artificial intelligence, and big data analysis, the accuracy and product quality of the production process are improved, and human errors are reduced.
Improve enterprise responsiveness: The flexible assembly system can quickly respond to changes in market demand, support rapid production conversion, and improve the company's ability to respond in the market.
Compared with traditional assembly lines, flexible assembly systems have more outstanding flexibility, adaptability, and intelligence. In modern manufacturing, with the rapid changes in market demand and the growing demand for personalized customization, flexible assembly system software is particularly important. Through intelligent and modular design, flexible assembly systems can improve production efficiency, reduce costs, and enhance the market competitiveness of enterprises. Therefore, more and more manufacturing companies choose flexible force control software to replace traditional assembly lines to meet the rapidly changing market and production needs.
Dapkon is a high-quality intelligent flexible robot technology and product provider. We are committed to cooperating with industry partners such as polishing, assembly, gluing, and testing through self-developed robot flexible control, multi-sensor fusion, and AI self-learning, combined with rich industry experience, empowering traditional robots, solving the pain points of difficult programming and complex deployment, and improving robot deployment efficiency; at the same time, combined with real-time data monitoring and force control perception, provide tool management functions such as consumable wear monitoring, compensation and protection, and improve the utilization rate of consumables; improve production processes through the accumulation and self-learning of real-time robot operation data.
www.dapkon.ai
Shanghai Dapkon Technology Co., Ltd.