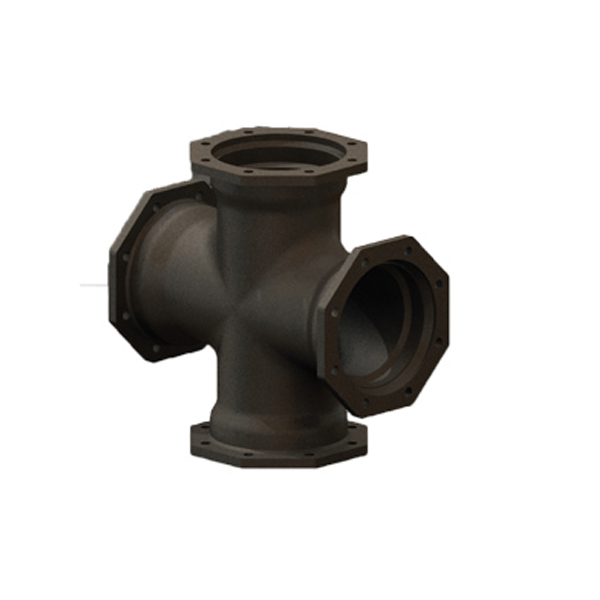
In the intricate world of structural engineering, the choice between bolted and welded joints is a critical decision that significantly impacts the integrity and functionality of a structure. In this exhaustive exploration, we will delve into the diverse types of bolted and welded joints, unraveling the complexities and applications that make each type unique.
I. Bolted Joints: A Spectrum of Connections
Bolted Flange Joints:
Flange joints, secured by bolts, are a common choice in industries requiring ease of assembly and disassembly. This type of bolted joint finds extensive use in piping systems, where modularity and adaptability are paramount. The precision of bolted flange joints ensures a secure connection while allowing for efficient maintenance.
Through-Bolted Joints:
Through-bolted joints involve bolts passing entirely through the components being connected. This method is favored in situations where high tension forces need to be distributed evenly. It is commonly employed in applications such as structural steel connections, providing a robust and reliable solution.
Tension Control Bolts (TCB):
Tension control bolts offer a unique advantage by providing a pre-tensioned connection. The controlled tension ensures uniform force distribution, reducing the risk of joint failure. TCBs are often chosen for applications where vibration resistance and durability are crucial, such as in bridges and high-rise buildings.
II. Welded Joints: Precision in Fusion
Butt Weld Joints:
Butt weld joints involve the fusion of two components at their ends. This method ensures a seamless and continuous connection, making it a preferred choice in applications demanding high structural integrity. Butt welds are commonly used in construction projects, such as the fabrication of steel beams and columns.
Fillet Weld Joints:
Fillet weld joints are characterized by a triangular cross-section and are employed to join two surfaces at right angles. This type of weld is versatile and finds use in a variety of applications, from simple structures to complex frameworks. Fillet welds are known for their efficiency in resisting shear and tensile forces.
Plug and Slot Welds:
In situations where components need to be joined through holes or slots, plug and slot welds come into play. These welds provide a strong connection while maintaining a streamlined appearance. They are commonly used in the automotive and aerospace industries for joining sheet metal components.
III. Choosing the Right Joint for the Job: Factors to Consider
The selection between bolted and welded joints is contingent on various factors, including load requirements, material compatibility, environmental conditions, and project specifications. Engineers must carefully evaluate these considerations to make informed decisions that align with the structural needs of their projects.
IV. Future Trends: Innovations in Joint Technology
As technology continues to advance, new innovations in joint technology emerge. From smart bolts that monitor structural health to advanced welding techniques, the future holds exciting possibilities for enhancing the efficiency and reliability of structural connections.
V. Conclusion: Navigating the Structural Landscape
In conclusion, the world of bolted and welded joints is expansive and diverse. Each type of joint offers unique advantages, and the key lies in understanding the specific demands of a project. This guide serves as a roadmap for engineers, providing insights into the intricacies of bolted and welded joints and empowering them to make decisions that stand the test of structural challenges.