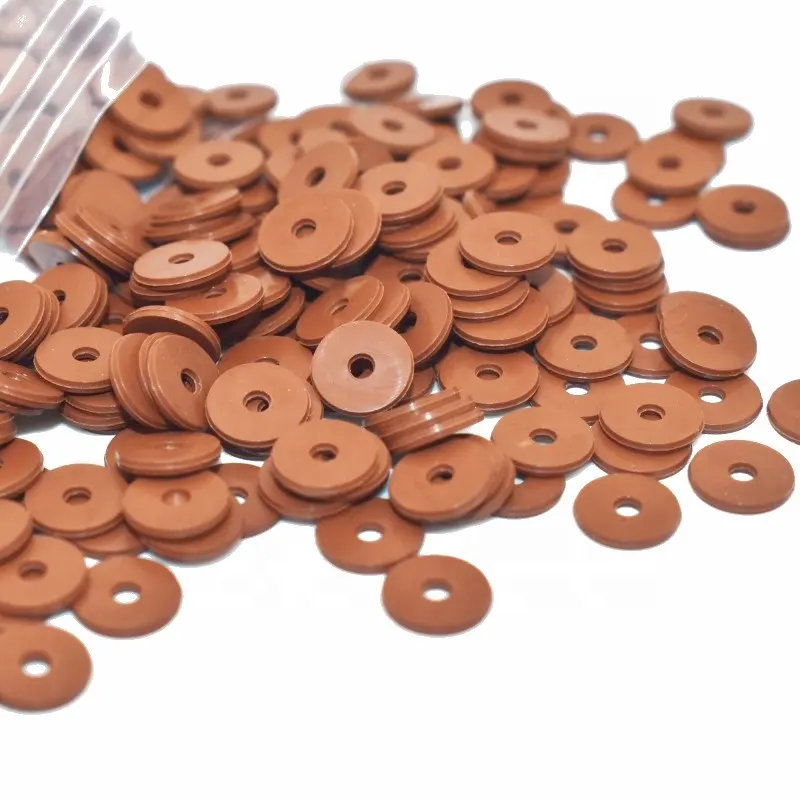
In industries where high temperatures are the norm, the integrity of seals is paramount. High temperature rubber gasket materials are engineered to provide exceptional performance and reliability in these demanding conditions. As a critical component in various mechanical and industrial systems, these gaskets must withstand thermal stress, maintain their physical properties, and prevent leaks effectively. This blog post will delve into the technical aspects of high temperature rubber gasket materials, their importance in harsh environments, and the factors that define their performance.
Understanding High Temperature Rubber Gasket Materials
High temperature rubber gasket materials are specially formulated to maintain their elasticity, resilience, and sealing efficiency at elevated temperatures. These materials are crucial in applications where standard rubber compounds would degrade or fail.
Key Characteristics of High Temperature Rubber Gasket Materials
Thermal Stability
The material must remain stable and not degrade when exposed to high temperatures, maintaining its physical properties over time.
Chemical Resistance
Resistance to chemicals is essential, as many industrial processes involve corrosive substances that can deteriorate standard rubber materials.
Compressibility
The gasket material should be compressible enough to fill gaps and create a seal but also resilient enough to return to its original shape after stress is removed.
Flame Resistance
In environments where there is a risk of fire, the gasket material must be self-extinguishing and not contribute to the spread of flames.
Ozone Resistance
Ozone can cause cracking in rubber materials; thus, resistance to ozone is a critical characteristic for gaskets used in outdoor applications or areas with high ozone levels.
Technical Specifications of High Temperature Rubber Gasket Materials
When evaluating high temperature rubber gasket materials, consider the following technical specifications:
Temperature Range
The material should be able to operate within a specified temperature range, from low-temperature flexibility to high-temperature resistance.
Tensile Strength
The material must have sufficient tensile strength to withstand the stress of compression and tension without breaking or deforming.
Elongation at Break
This property indicates the material's ability to stretch before breaking, which is important for creating a secure seal under pressure.
Hardness
The Shore hardness of the material affects its compressibility and resilience, with different applications requiring different hardness levels.
Compression Set
The material's resistance to permanent deformation under sustained compression is crucial for maintaining a long-term seal.
Thermal Conductivity
In some applications, the ability of the material to conduct heat can be beneficial for temperature management.
Electrical Insulation
For applications involving electrical components, the gasket material should provide insulation to prevent short circuits.
Types of High Temperature Rubber Gasket Materials
Several types of high temperature rubber gasket materials are available, each with its own set of properties and applications:
Silicone Rubber
Silicone rubber is known for its excellent resistance to high temperatures, ozone, and weathering. It remains flexible over a wide temperature range.
Fluoroelastomers (FKM/Viton®)
Fluoroelastomers offer superior resistance to heat, chemicals, and oxygen. They are suitable for use in aggressive chemical environments and high-temperature applications.
Ethylene-Propylene-Diene Monomer (EPDM)
EPDM is resistant to heat, ozone, and weathering, making it a popular choice for outdoor applications and automotive components.
Perfluoroelastomers (FFKM)
Perfluoroelastomers provide the highest level of resistance to chemicals, heat, and solvents, making them suitable for the most demanding applications.
Kalrez® Perfluoroelastomer
Kalrez® is a unique perfluoroelastomer that offers excellent chemical resistance and high-temperature performance, suitable for use in the chemical processing and semiconductor industries.
Applications of High Temperature Rubber Gasket Materials
High temperature rubber gasket materials are used in a variety of applications where heat resistance is critical:
Automotive Industry
In engines, exhaust systems, and turbochargers, high temperature gaskets ensure sealing and reliability.
Chemical Processing
In chemical plants, gaskets must resist corrosion from a wide range of chemicals and maintain their integrity at high temperatures.
Power Generation
In power plants, gaskets are used in steam turbines, boilers, and other high-temperature equipment to prevent leaks and ensure safety.
Aerospace Industry
Aerospace applications require gaskets that can withstand extreme temperatures and maintain their properties in varying environmental conditions.
Food and Beverage Industry
In food processing equipment, high temperature gaskets must be resistant to heat and withstand frequent sterilization processes.
Challenges and Considerations in High Temperature Rubber Gasket Materials
Several challenges and considerations arise when working with high temperature rubber gasket materials:
Material Selection
Selecting the appropriate material for a specific application requires knowledge of the temperature, chemical exposure, and pressure conditions.
Design and Engineering
Gasket design must consider factors such as bolt torque, flange configuration, and stress relaxation to ensure a reliable seal.
Installation
Proper installation is critical to prevent damage to the gasket, which could lead to leaks or failure.
Maintenance and Inspection
Regular inspection and maintenance are necessary to identify signs of wear or degradation and replace gaskets before they fail.
Regulatory Compliance
Gasket materials must comply with industry standards and regulations, including those related to food safety, environmental emissions, and worker safety.
Future Trends in High Temperature Rubber Gasket Materials
The field of high temperature rubber gasket materials is constantly evolving, with several trends shaping the future:
Material Innovations
New materials and formulations are being developed to provide improved resistance to heat, chemicals, and environmental stressors.
Sustainability
There is a growing focus on the development of more sustainable materials, including those that are recyclable or made from renewable resources.
Digitalization
Digital technologies, such as simulation software, are being used to optimize gasket design and predict the performance of materials under various conditions.
Automation and Robotics
Automation in the manufacturing process can improve the consistency and quality of gaskets, reducing the potential for defects.
Performance Testing
Advanced testing methods are being developed to better understand the behavior of materials under extreme conditions, leading to more reliable gasket designs.
Conclusion
High temperature rubber gasket materials are essential in ensuring the reliability and safety of equipment in harsh environments. As technology advances and industries demand higher performance, the development of innovative materials and designs will continue to be crucial. By understanding the technical aspects, challenges, and future trends, manufacturers and engineers can select the most appropriate gasket materials for their applications, ensuring the highest level of performance and safety.
www.allaboutrubber.com
Zhengli