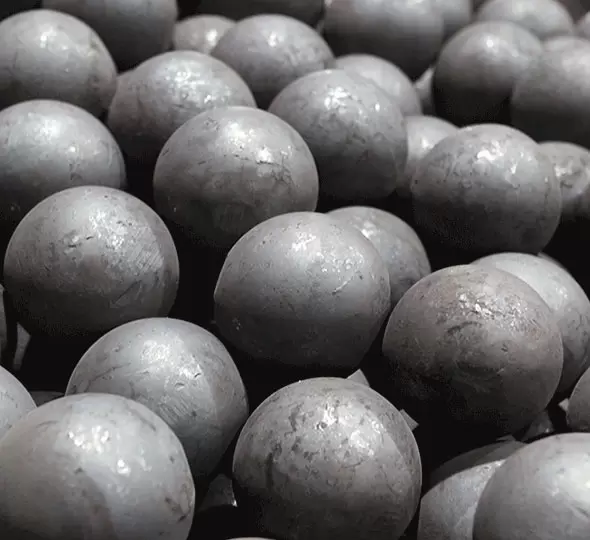
In modern industrial production, wear is a significant factor affecting efficiency and cost. As a consumable material with excellent wear resistance, the hot forged grinding ball plays an indispensable role in mining, cement, thermal power generation, chemical industry, and other industries. With its unique production process and outstanding performance, it demonstrates excellent stability in high-load and high-impact working environments. In this article, Longteng will thoroughly analyze the process characteristics of the hot forged grinding ball.
What is a Hot Forged Grinding Ball?
A hot forged grinding ball is a high-strength metal ball made through a forging process, primarily used for crushing and grinding ore, coal, cement raw materials, and other materials in ball mills. Its manufacturing process involves high-temperature heating, forging, and heat treatment. Through these steps, the hot forged grinding ball achieves excellent hardness, impact resistance, and wear resistance, maintaining long-term stable operation in high-intensity grinding environments.
Compared with traditional cast grinding balls, hot forged grinding balls offer significant performance advantages. The internal structure of cast grinding balls may contain defects such as pores and shrinkage cavities, while the hot forged grinding ball is compressed by strong external force during the forging process, resulting in a denser internal structure that eliminates such defects. This high density not only provides the hot forged grinding ball with superior strength and toughness but also makes it less prone to breaking or failing during use.
Additionally, the surface hardness and core hardness of the hot forged grinding ball are evenly distributed, providing excellent wear resistance in both high-speed rotating mills and high-impact crushing environments. Whether it involves grinding high-hardness ores in mining or intense powder grinding in cement production, hot forged grinding balls meet stringent operational requirements with stable performance and a long service life.
Process Characteristics of Hot Forged Grinding Balls
The exceptional performance of hot forged grinding balls is closely linked to their complex and precise production process. From the selection of raw materials to the quality inspection of the final product, every step directly impacts the performance of these grinding balls.
1. Material Selection
The selection of materials is the first critical step affecting the performance of hot forged grinding balls. These balls typically use high-carbon steel or alloy steel as raw materials, which offer high hardness and excellent mechanical properties. To further enhance wear and impact resistance, alloy elements such as chromium, manganese, and molybdenum are added during production.For example, high-chromium steel hot forged grinding balls are commonly used for grinding high-hardness ores due to their extremely high surface hardness and excellent wear resistance. While low-chromium steel hot forged grinding balls have slightly lower hardness, their balanced comprehensive performance makes them suitable for general working conditions, offering higher cost-effectiveness. Different material compositions enable the customization of hot forged grinding balls according to specific requirements, ensuring optimal performance.
2. High-Temperature Heating and Forging
The production process requires heating the metal billet to the forging temperature (typically 950°C to 1050°C). At such high temperatures, the metal's plasticity increases significantly, while deformation resistance decreases, allowing it to be shaped more easily under the high pressure of forging equipment.The core of the forging process involves applying strong external forces to continuously hammer or compress the metal billet, refining its internal grains and eliminating potential pores and cracks, thus forming a dense structure. This density significantly enhances the wear and impact resistance of hot forged grinding balls, reducing the likelihood of breakage in high-intensity grinding environments.
3. Heat Treatment Process
After forging, hot forged grinding balls undergo heat treatment processes such as quenching and tempering to optimize hardness and toughness. The quenching process enhances surface hardness, improving wear resistance, while tempering relieves internal stress generated during quenching, ensuring sufficient core toughness and impact resistance.A well-designed heat treatment process also ensures uniform hardness distribution, extending the ball's service life under high-wear and high-impact conditions. This feature is particularly valuable in grinding hard rocks in the mining industry and coal powder preparation in thermal power plants.
4. Strict Quality Inspection
To ensure each batch of hot forged grinding balls meets high-performance standards, rigorous quality inspections are conducted during production. These include hardness testing, metallographic analysis, impact resistance testing, and size measurements. These inspections help detect and eliminate potential quality issues, ensuring that the grinding balls consistently perform well in various working conditions.
With their high strength, exceptional wear resistance, and superior impact resistance, hot forged grinding balls have become indispensable consumables in modern industrial grinding processes. From mining to cement production, and from thermal power generation to chemical manufacturing, hot forged grinding balls provide a robust guarantee for efficient production in numerous industries. Through strict process control and precise quality inspections, these grinding balls demonstrate significant performance advantages and generate substantial economic benefits for users.In future industrial applications, hot forged grinding balls will continue to play an irreplaceable role, contributing to the sustainable development of various industries.
https://www.lttgsteel.com/Hot-Rolled-and-Hot-Forged-Grinding-Balls/
www.lttgsteel.com
Jiangsu Longteng Special Steel Group