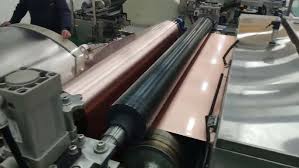
Electrolytic copper foil plays a crucial role in various industries, particularly in lithium battery production, printed circuit boards (PCBs), and electromagnetic shielding applications. Given its critical applications, ensuring the quality of electrolytic copper foil is paramount. A well-structured test process is essential to maintain high standards of thickness uniformity, mechanical properties, conductivity, and overall reliability. This article provides a detailed breakdown of the test process involved in an electrolytic copper foil test line.
1. Raw Material Inspection
Before the electrolytic deposition process begins, the raw materials, primarily copper cathodes and electrolytes, must be tested for purity and consistency.
Copper Purity Test: The raw copper is analyzed using spectroscopy methods such as Inductively Coupled Plasma Optical Emission Spectroscopy (ICP-OES) to ensure it meets industry standards (typically 99.99% purity).
Electrolyte Analysis: The composition of the sulfuric acid and copper sulfate solution is measured to ensure proper ion concentration for consistent electrolysis.
2. Electrolytic Deposition Process Monitoring
During the production of electrolytic copper foil, various real-time monitoring mechanisms ensure the correct deposition rate and quality.
Thickness Control: Laser or X-ray thickness gauges continuously measure the foil to ensure uniformity.
Surface Inspection: Optical and camera-based inspection systems detect defects such as pinholes, cracks, or uneven surfaces.
Tensile Strength and Ductility Testing: Real-time tensile testing ensures the mechanical properties meet required standards.
3. Post-Production Testing
Once the copper foil is produced, it undergoes a series of quality checks to verify its suitability for industrial applications.
a) Thickness Measurement
Thickness is a critical factor that determines the foil's performance in applications such as batteries and PCBs. Methods used include:
X-ray Fluorescence (XRF): Provides accurate, non-destructive measurement of foil thickness.
Micrometer Measurement: A high-precision mechanical gauge measures sample pieces for validation.
b) Surface Roughness Analysis
The surface roughness of the copper foil affects adhesion properties in PCB and lithium battery applications. Testing includes:
Atomic Force Microscopy (AFM): Measures micro-level surface roughness.
Stylus Profilometry: A mechanical stylus runs across the surface to measure irregularities.
c) Tensile and Elongation Tests
Mechanical properties such as tensile strength and elongation rate impact durability and flexibility.
Universal Testing Machines (UTM): Apply controlled force to measure tensile properties.
Elongation Measurement: Ensures the foil can withstand stretching without breaking.
d) Electrical Conductivity Testing
Copper foil must have excellent conductivity to ensure minimal resistance in electronic applications.
Four-Point Probe Method: Measures electrical resistivity accurately.
Eddy Current Testing: A non-destructive method to assess conductivity consistency.
e) Adhesion and Peel Strength Tests
For applications like PCBs, the foil must adhere well to substrates.
Peel Strength Test: Measures the force required to peel the foil from a test substrate.
Adhesion Tape Test: Uses adhesive tape to test surface adhesion properties.
4. Chemical Resistance and Corrosion Testing
To ensure long-term reliability, copper foils undergo tests to assess their resistance to environmental factors.
Salt Spray Test (ASTM B117): Simulates harsh environmental exposure to check corrosion resistance.
Acid and Alkali Resistance: Evaluates the foil’s ability to withstand chemical exposure.
5. Final Inspection and Quality Certification
After passing all individual tests, the final batch undergoes:
Batch Consistency Checks: Ensuring uniformity across the production batch.
Certification and Compliance Tests: Meeting international standards such as ASTM, IPC, and IEC.
Packaging Inspection: Verifying proper handling to prevent damage during transportation.
Conclusion
A comprehensive electrolytic copper foil test process ensures that the final product meets stringent quality standards. By implementing precise testing procedures at each stage—from raw material selection to post-production analysis—manufacturers can guarantee high-performance copper foil for lithium batteries, PCBs, and other critical applications.
About Timonic
Timonic (Suzhou) Technology Co., Ltd. (Timonic), a subsidiary of China Special Metal Group Limited (CSM), is dedicated to the development and production of new energy lithium battery material production equipment. Our expertise includes lithium battery copper foil machines, cathode rolls, and customized solutions for high-quality lithium copper battery foil plants. Timonic provides one-stop services, including plant design, intelligent mechanical and electrical equipment, automation systems, and technical support to ensure top-tier quality control in copper foil manufacturing.
Necessity And Advantages of Customized Electrolytic Copper Foil Test Line
www.timonic.com.cn
Timonic (Suzhou) Technology Co., Ltd