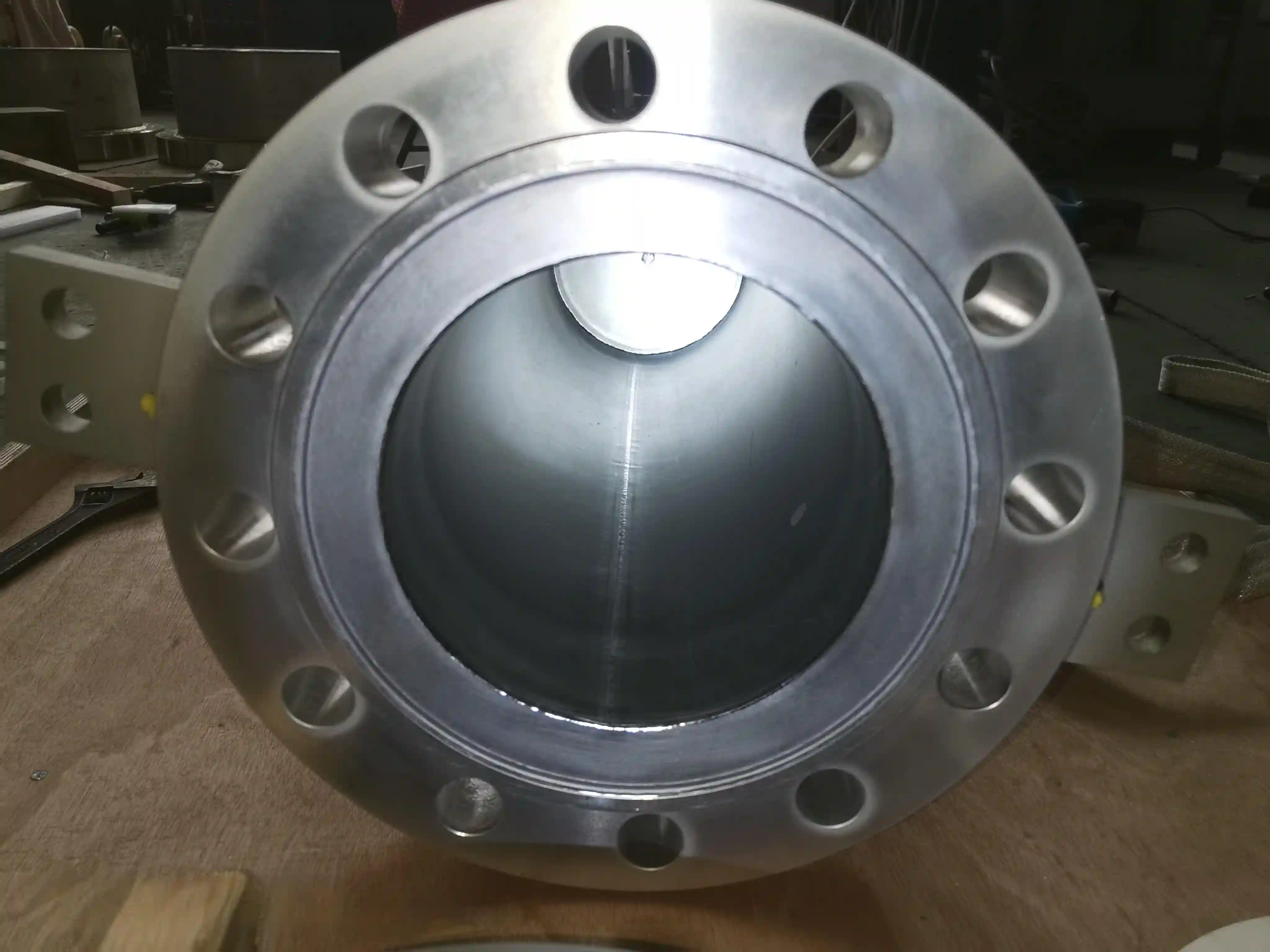
Tantalum lined pressure vessels represent a significant advancement in materials engineering, designed to meet the demanding requirements of industries where corrosive substances are prevalent. These vessels are constructed with a tantalum lining that provides unparalleled resistance to corrosion, making them ideal for applications in chemical processing, pharmaceuticals, and other sectors that handle aggressive media. The unique properties of tantalum, combined with advanced manufacturing techniques, allow these pressure vessels to maintain integrity under extreme conditions, thereby ensuring safety and reliability. By integrating tantalum into the design of pressure vessels, industries can protect both their processes and personnel from the risks associated with corrosive materials.
Design Considerations for Tantalum Lined Pressure Vessels
1. Material Selection
The selection of materials for constructing a tantalum lined pressure vessel is critical. The base material, often carbon steel or stainless steel, must possess adequate strength to support the tantalum lining while ensuring overall structural integrity. The compatibility of the base material with the tantalum lining is also essential, as any galvanic corrosion between dissimilar metals could compromise the vessel’s performance. Proper selection can significantly influence the longevity and effectiveness of the vessel in corrosive environments.
2. Lining Thickness
The thickness of the tantalum lining is another important design consideration. While a thicker lining may provide enhanced corrosion resistance, it also adds to the overall weight and cost of the vessel. Engineers must balance these factors to determine the optimal lining thickness that meets the specific requirements of the application without incurring unnecessary expenses. A careful analysis of the chemical environment and expected operational conditions is crucial in making this decision.
3. Fabrication Techniques
The fabrication of tantalum lined pressure vessels requires specialized techniques to ensure proper bonding between the tantalum and the base material. Common methods include welding, cladding, and explosive bonding. Each technique has its advantages and limitations, and the choice of method will depend on factors such as vessel size, complexity, and intended use. The integrity of the bond between the tantalum and the substrate is vital to preventing delamination and ensuring long-term performance.
4. Pressure and Temperature Ratings
Determining the appropriate pressure and temperature ratings for tantalum lined pressure vessels is vital. These ratings must align with the specific operating conditions to ensure safe and efficient performance. Engineers typically conduct rigorous testing and calculations to ascertain the vessel's limits, taking into account factors such as internal pressure, temperature fluctuations, and the corrosive nature of the media being processed. Adhering to industry standards for pressure vessels is crucial to maintaining safety and regulatory compliance.
Applications of Tantalum Lined Pressure Vessels
1. Chemical Processing
In the chemical processing industry, tantalum lined pressure vessels are indispensable. They are commonly used to store and transport aggressive chemicals that would otherwise corrode conventional materials. The exceptional corrosion resistance of tantalum allows for safe handling of hazardous substances, thus ensuring compliance with safety regulations and protecting the environment. For example, vessels handling strong acids or solvents can maintain their integrity, preventing leaks that could lead to environmental contamination.
2. Pharmaceutical Manufacturing
The pharmaceutical industry benefits significantly from tantalum lined pressure vessels due to the material's biocompatibility and inert nature. These vessels are utilized in processes involving the production of active pharmaceutical ingredients (APIs) and other sensitive compounds. The ability of tantalum to maintain purity and prevent contamination is crucial in this sector, where product integrity is of utmost importance. Furthermore, tantalum lined vessels help ensure that production processes remain efficient and compliant with stringent regulatory requirements.
3. Aerospace Applications
Tantalum lined pressure vessels are increasingly being explored for aerospace applications, particularly in fuel systems and propulsion components. The high melting point and exceptional strength of tantalum make it suitable for extreme environments encountered during flight. Additionally, the corrosion resistance ensures that fuel systems remain reliable and safe under varied atmospheric conditions. The lightweight nature of tantalum also contributes to overall weight savings in aerospace design, enhancing fuel efficiency.
4. Nuclear Industry
In the nuclear industry, tantalum lined pressure vessels are used in systems that require containment of radioactive materials. The corrosion resistance of tantalum ensures the integrity of the vessel over long periods, mitigating the risk of leaks or failures that could have catastrophic consequences. This application highlights the critical role of tantalum in maintaining safety and reliability in sensitive environments, where even minor breaches can lead to significant safety concerns.
Tantalum lined pressure vessels exemplify engineering excellence, combining advanced materials with innovative design to meet the rigorous demands of corrosive environments. Their exceptional properties, including corrosion resistance, high melting point, and mechanical strength, make them indispensable in various industries such as chemical processing, pharmaceuticals, aerospace, and nuclear energy.As industries continue to seek reliable solutions for handling aggressive media, tantalum lined pressure vessels will play a critical role in ensuring safety, efficiency, and long-term performance in demanding applications.
https://www.tnztn.com/Tantalum-Lined-Vessel.html
www.tnztn.com
Wuxi Qiwei Nonferrous Technology Co., Ltd.